Aluminum beverage cans are the most sustainable beverage package on virtually every measure. Aluminum cans have a higher recycling rate and more recycled content than competing package types. They are lightweight, stackable and strong—allowing brands to package and transport more beverages using less material.
43%
Average greenhouse gas emissions reduction for an aluminum beverage can produced in North America since 1991.
12X
Aluminum cans contain 73% recycled content – 12X as much as plastic and 3X as much as glass.
38%
Weight reduction of the average aluminum beverage can since the 1970s – doing more with less.
Innovation in Action
Coors pioneered the use of aluminum cans in 1959. Since then, aluminum cans have become an increasingly popular package for consumers and companies alike. From craft beers and canned wine, to energy drinks and sparkling water—the opportunities for aluminum cans are endless.
The Aluminum Can Advantage
Aluminum beverage cans are the most sustainable beverage package on virtually every measure. Cans have a higher recycling rate and more recycled content than competing package types. They are lightweight, stackable and strong, allowing brands to package and transport more beverages using less material. And aluminum cans are far more valuable than glass or plastic, helping make municipal recycling programs financially viable and effectively subsidizing the recycling of less valuable materials in the bin.
Most of all, aluminum cans are recycled over and over again in a true "closed loop" recycling process. Glass and plastic are typically "down-cycled" into products like carpet fiber or landfill liner.
The Aluminum Association releases an annual Key Performance Indicator (KPI) report tracking a number of metrics on the can's sustainability performance compared to competing packaging types.
Smart Design for Recycling
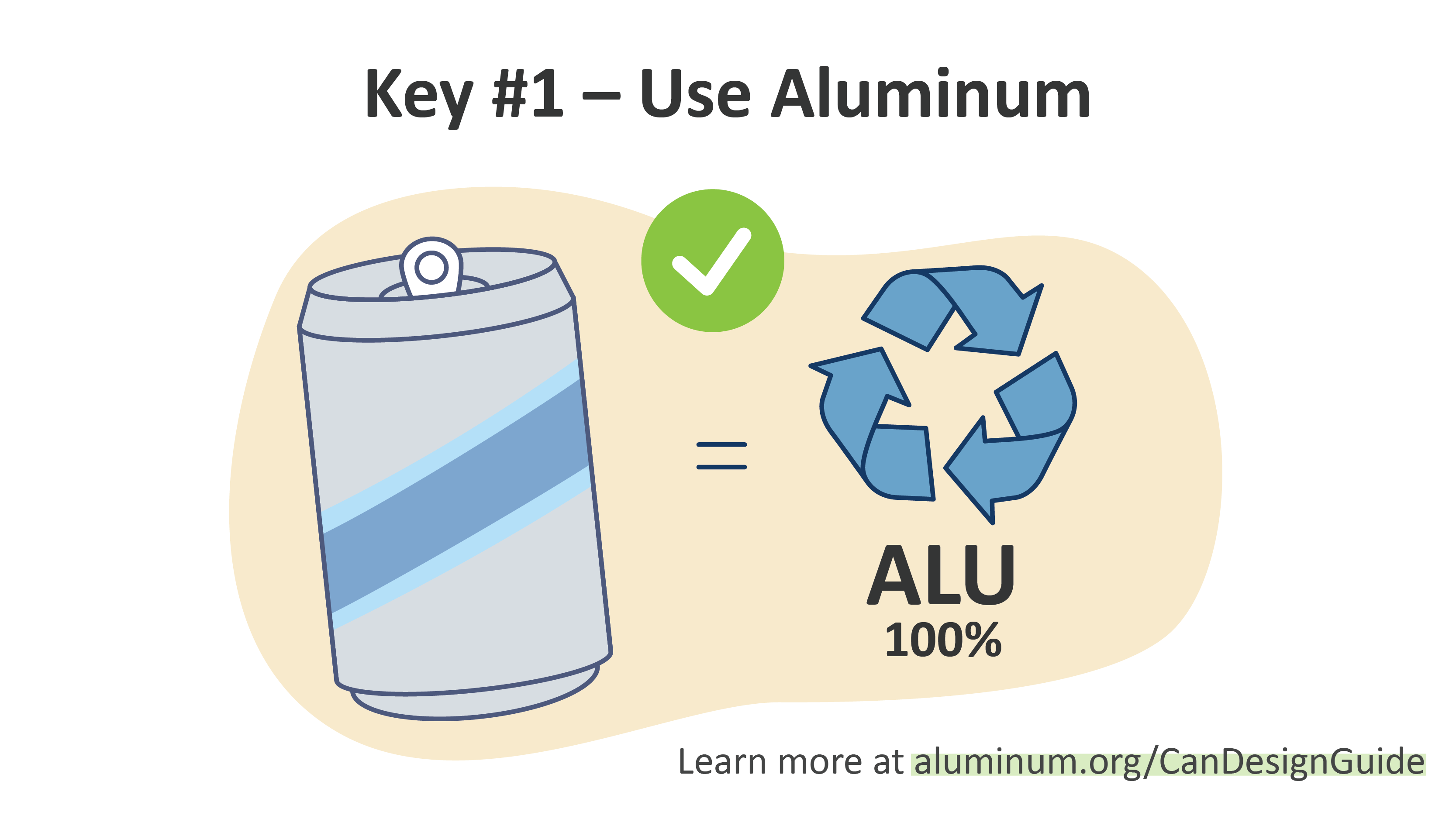
The growing use of aluminum cans, particularly in the craft beer market, has driven an increase in plastic (rather than ink) and labeling on aluminum beverage cans. While convenient, these labels—along with other plastic components added to cans—hurt recycling efforts by diluting the value of aluminum can recycling and causing operational and compliance problems for recyclers. The good news is that new technologies like affordable ink jet printing for small batch canning allows companies to easily label their cans while avoiding recycling pitfalls.
The Aluminum Association developed Four Keys to Circular Recycling: An Aluminum Container Design Guide to highlight these issues and recommend best practices for how beverage companies and container designers can best use aluminum in its product packaging.
Related News & Resources