
Powering Up American Aluminum: A Roadmap for Next Generation Supply Chain Resilience
The aluminum industry needs access to a reliable metal supply and abundant, affordable energy to continue to grow and expand in the United States. A new white paper, developed by the Aluminum Association and Wittsend Commodity Advisors, lays out potential pathways to move the U.S. aluminum industry toward greater domestic self-sufficiency.
Essential American Industry
Aluminum is a critical material for our nation’s economic and national security. It's in everything – from cars and cans to fighter jets, tanks and the electric grid. The aluminum industry supports nearly 700,000 jobs and generates more than $228 billion in economic impact. In 2024, key sectors across the aluminum industry (recycling & sheet/plate) saw record jobs since the Aluminum Association began tracking in 2013. At the same time, the industry has invested more than $10 billion in U.S. operations over the last decade, including two new aluminum rolling mills for the first time since 1980.
The U.S. aluminum industry looks very different today than it did 25 years ago, but it continues to pursue generational investment.
Since 2000:
- Operating U.S. primary aluminum smelters declined from 24 to 4 today due to lack of low-cost domestic electricity and unfair trade practices in China
- North America went from producing the most primary aluminum on earth to 4th place today with output dwarfed by China
- Demand for aluminum grew consistently as the U.S. industry evolved and shifted its business mid-and-downstream
- Domestic aluminum recycling grew by ~1/3 and now accounts for ~85% of U.S.-made aluminum
- Nearly 98% of all U.S. aluminum jobs today are in mid-and-downstream processing and recycling.
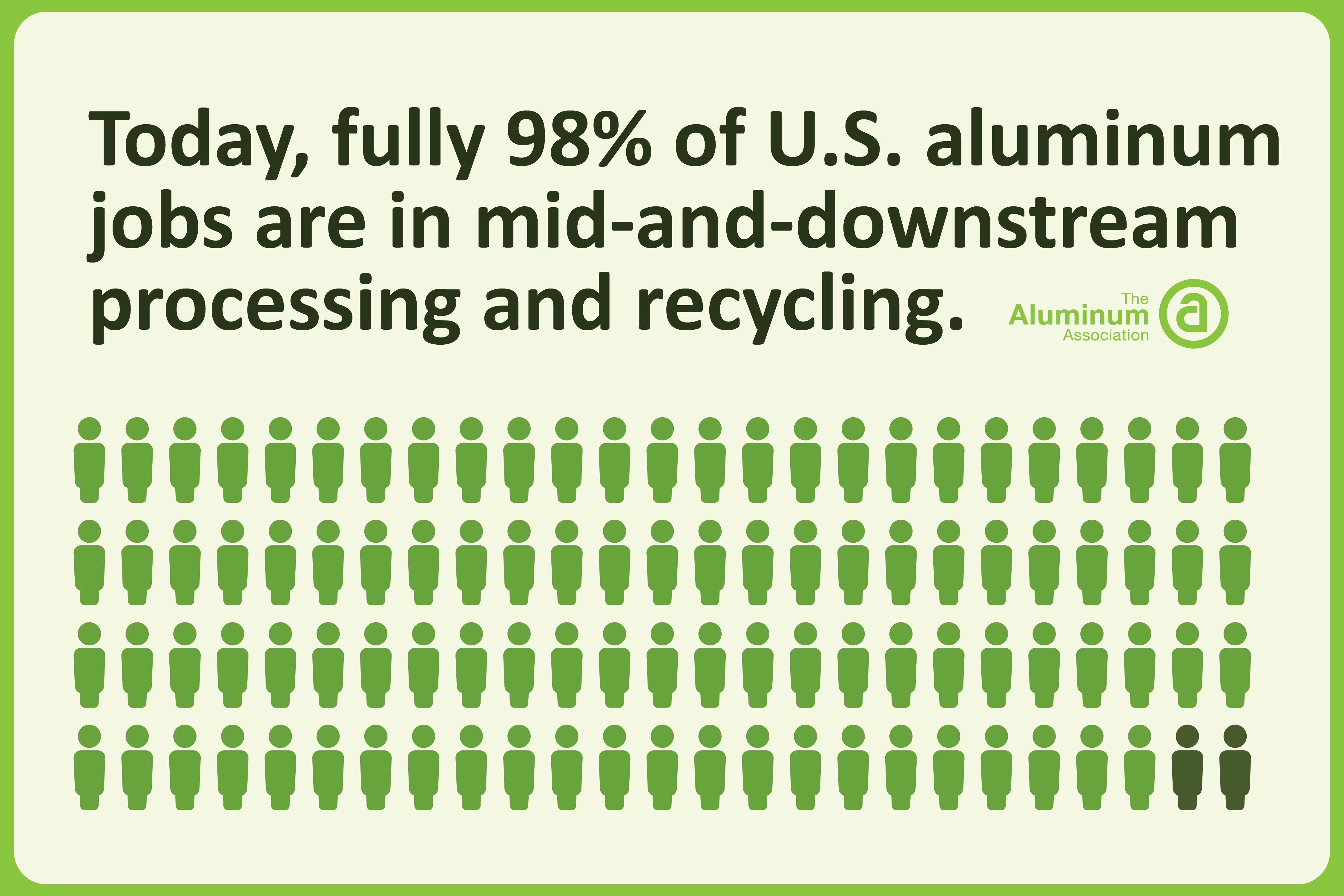
Despite a ~70% decline in primary aluminum jobs since 2013, overall industry jobs are effectively flat as employment shifted downstream and certain industry segments have seen record job growth. Strong trade enforcement including Section 232, Section 301 and antidumping/countervailing duty tariff interventions during the first Trump administration supported this growth.
Pathways to Self-Sufficiency
Achieving U.S. aluminum self-sufficiency will require time, money and commitment from both the public and private sector to build new smelters and recycle more aluminum. Powering Up American Aluminum: A Roadmap for Next Generation Supply Chain Resilience, developed by the Aluminum Association and Wittsend Commodity Advisors, lays out three potential pathways to move the U.S. aluminum industry toward greater domestic self-sufficiency.
The white paper focuses on:
New: There are undoubtedly opportunities to build new aluminum smelting capacity in the United States, including two projects currently under discussion. Building such facilities will take time (5 – 6 years), significant capital investment ($4 - $6 billion/facility) and long-term, competitive power contracts and the equivalent annual electricity usage of the city of Boston or Nashville. To fully meet current metal needs, the United States would need to build around five 750,000 metric ton smelters. The largest fully operational smelter in the United States right now is 220,000 metric tons.
Restart: Slightly less than half of installed U.S. primary aluminum capacity is currently in operation. Bringing this metal back online from 4 existing smelters would require long-term, competitively priced power contracts and still significant capital investment. Even then, restarting all idled smelters would only meet around 15% of the current 4 million metric ton metal supply gap.
While domestic primary production has declined over recent decades, recycled (or secondary) aluminum production has grown, hitting record levels in 2024. Recycling aluminum is about 95% less energy intensive than primary production and relies largely on scrap aluminum as an input material. Building aluminum recycling facilities is also far less capital intensive. New sorting technologies could unlock even more available scrap aluminum. Collecting and recycling the estimated 1 - 2 million MT of usable scrap currently landfilled or exported would meet 25% - 50% of the existing U.S. metal supply gap.
As the industry works to produce more domestic aluminum, access to affordable, reliable Canadian primary aluminum is a vital bridge for metal supply and a good deal for America. The aluminum the United States imports from Canada is equivalent to more than 4 Hoover Dams worth of energy each year – often at a significant discount from direct electricity imports. Aluminum smelters in Canada typically pay $25 - $40 per MWh of electricity vs. $60 - $80 per MWh in the United States. Further, every one aluminum smelter job in Canada supports about 13 U.S. aluminum jobs further downstream.
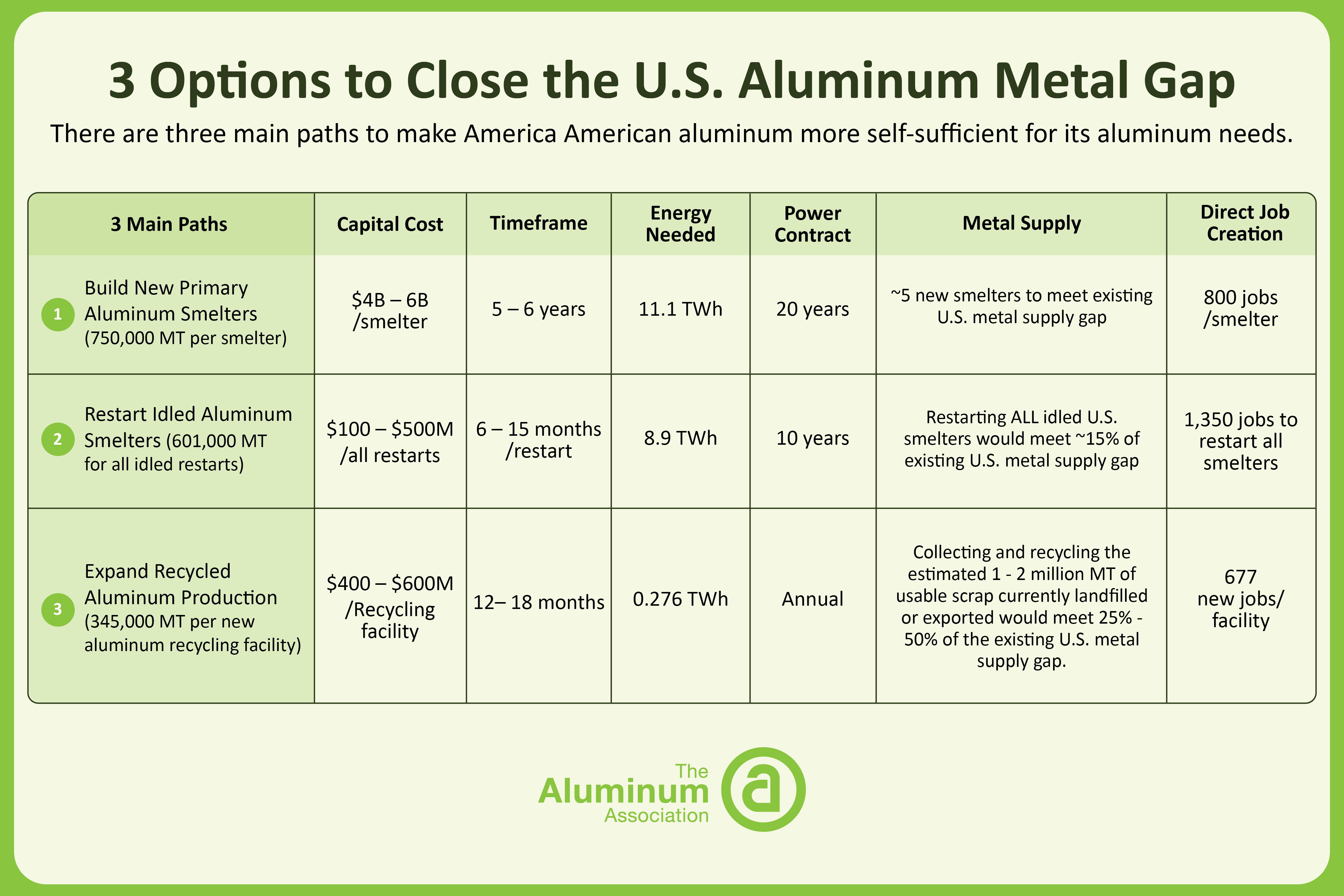
Enormous electricity requirements for primary aluminum production poses a unique challenge for industry self-sufficiency. A single new aluminum smelter uses ~11 TWh – a similar amount of electricity every year as a major U.S. city like Boston or Nashville. Furthermore, to be economically competitive, a smelter requires a 10 – 20 year contract with electricity costs ~$40/MWh. Technology companies are currently committing upward of $115/MWh for power at AI data centers. The Energy Information Administration estimates that the United States will have an energy deficit ~ 50 TWh by 2035 on current trendlines.
Policies to Support Great American Self-Reliance
Energy/Manufacturing
- Promote affordable, long-term energy supply growth for manufacturers using an ‘all of the above’ approach to fuel sourcing
- Provide incentives for optimization of existing energy supply including:
- Turbine upgrades for hydropower efficiency improvements
- Extension of nuclear facility operating licenses
- Fossil fuel fired base load capacity retention
- Exploration/production growth on public and private land
- Promote growth of new energy supplies via:
- Innovative uses of public-private partnerships
- Expanded production and investment tax credits
- Expedited permitting and licensing for new projects and technologies like small modular reactors
- Provide incentives for optimization of existing energy supply including:
- Expand accessibility of energy supplies
- Expedite interconnection of new electricity generation facilities to the grid - reducing the interconnection queue of 2,289 GW of power supply awaiting connection at the end of 2024
- Remove barriers to competitive bidding of new electrical transmission line installation, such as incumbent utility Right of First Refusal programs
- Expand grid enhancing technologies like dynamic line ratings
- Pursue permitting reform for energy and manufacturing projects to streamline new project construction
- Incentivize the timeliness, predictability, and transparency of regulatory agency permitting actions
- Expand FAST-41 Act and similar state programs for permitting improvements
- Support policies that grow US natural gas production, incentivize new natural gas pipeline construction, and optimize existing natural gas pipeline use to meet the needs of the domestic manufacturing base
- Invest in existing and new recycling infrastructure for collection and sorting so more energy-saving recyclable material can be used as an input material
Trade
- Ensure tariff-free access to Canadian aluminum imports to support U.S. metal demand.
- Expand the list of aluminum derivative products covered under Section 232 tariffs.
- Enforce existing USMCA protections and strengthen monitoring and enforcement to protect North American manufacturing from unfairly traded metal and circumvention.
Recycling
- Increase the availability of scrap aluminum to manufacturers:
- Invest in new recycling infrastructure including technology to sort recyclable metal so that it can be used as input material.
- Encourage recycling through consumer-facing collection infrastructure and state policies that create financial incentives to recycle.
- Support policies that keep scrap aluminum at home for domestic consumption and production.
Learn More