Aluminum Fast Facts
The Aluminum Production Process
Aluminum is the most abundant metal in the earth’s crust and is equally abundant in our everyday life—from kitchen foil to beverage cans to airplanes to automobiles. The modern aluminum production process from bauxite mining to refining to production to recycling has changed the way the world operates. Here’s how the process works – from bauxite mining to product recycling and back again.
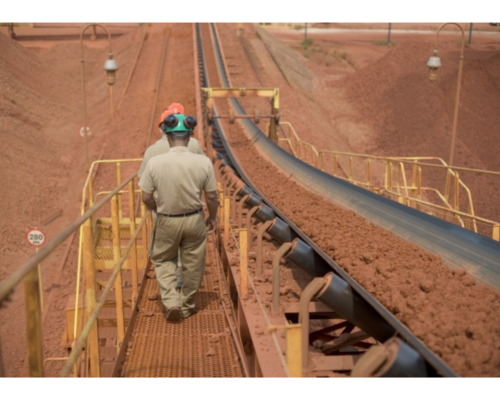
Bauxite
Bauxite ore is the world’s primary source of aluminum. Bauxite reserves are found in topsoil and are most plentiful in Africa, Oceania and South America. Reserves are projected to last for centuries
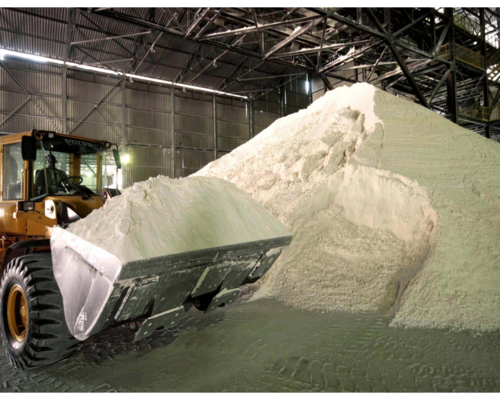
Alumina Refining
Alumina is the common name given to aluminum oxide (Al2O3). Alumina is produced from bauxite via the Bayer process, which is the primary process by which alumina is extracted from bauxite.

Primary Production
Primary production is the process by which alumina is smelted to pure aluminum metal. The Hall–Héroult process, simultaneously discovered in 1886 by American Charles Martin Hall and Frenchman Paul Héroult, continues as the main industrial process by which primary aluminum is made
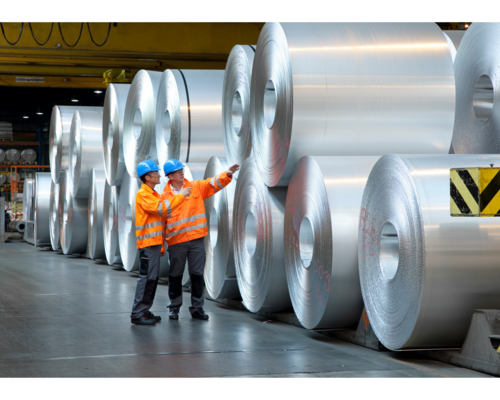
Processing
Between the production of aluminum from bauxite to well-known end products lies processing. The processing of aluminum—using castings, extrusions and mill products—allows the industry to support end users to become more innovative with their designs and utilize greater technologies.
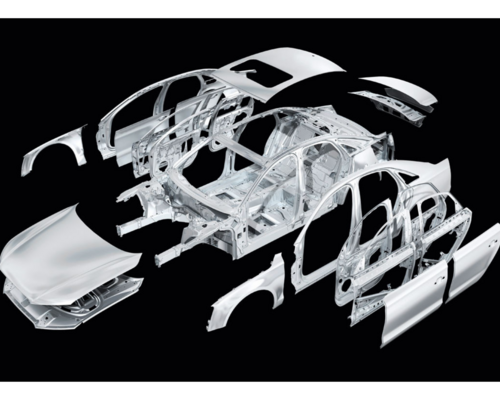
Product Markets
Aluminum is all around us, making our everyday lives easier and more efficient. Aluminum sent us to Mars, motors us to greater fuel-and cost-efficient vehicles, increases our buildings’ energy efficiency and facilitates our productivity through our iPads, smartphones and laptops
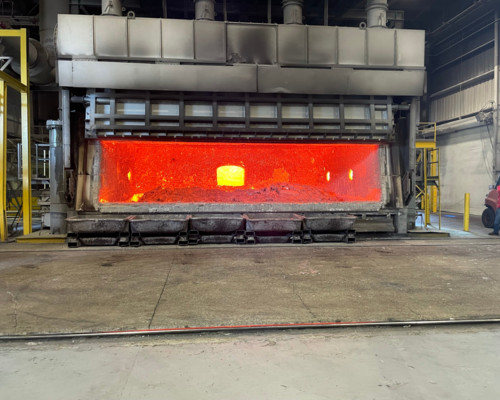
Secondary Production
Secondary Production is the process of recycling aluminum scrap into aluminum that can be used again—an environmentally sound process. More than 80 percent of U.S. production today is in making recycled (or secondary) aluminum, up from 20-30 percent recycled production in the 1980s.
History of Aluminum
Aluminum’s impact over the past 100 years has been so profound that historians may one day look back on our times and declare this “The Age of Aluminum.”
The start was a modest one, however. A pure form of the metal was first successfully extracted from ore in 1825 by Danish chemist Hans-Christian Oersted. The most abundant metal in the earth’s crust, metallic aluminum is never found in its pure form. It is always chemically bound with other elements, such as oxygen or chlorine. Due to the complexities of refining aluminum from ore, aluminum was considered more rare and precious than gold or silver through most of the 19th century.
In fact, Napoleon III loved the stuff so much he would serve his most honored guests on plates made from aluminum.
Aluminum: The choice of presidents
Napoleon III, the first president of the French Republic, served his state dinners on aluminum plates. Rank-and-file guests were served on dishes made with gold or silver.
The Great Depression set the stage
The Works Progress Administration hydroelectric projects started during the Great Depression were key to developing the electrical capacity needed for industrial-class aluminum production in the US.
1933: The Aluminum Association is founded
In 1933, President Franklin Roosevelt signed the National Industrial Recovery Act, asking industries to establish guidelines for fair competition. The Aluminum Association’s first meeting was held in New York City in October 1935.
Aluminum goes to the moon
Human flight was made possible by aluminum. From the Wright brothers through Sputnik, to the Apollo Space Program and beyond, aluminum has been essential for major advances in aerospace technology and accomplishment.
During ancient times, aluminum oxide clays were used in hide tanning, first aid, fabric dying and fireproofing.
These major milestones occurred during aluminum’s “discovery period”:
- 1865: Science fiction writer Jules Verne describes an aluminum space rocket in his novel, Journey to the Moon.
- 1886: Oberlin College student Charles Hall and French engineer Paul Heroult separately and simultaneously develop an efficient electrolysis process by which aluminum can be extracted from aluminum oxide. The large amount of electricity required to power the electrolytic process limited the production of aluminum. Hall received U.S. patent #400,666 in 1889.
- 1887: Austrian engineer Karl Josef Bayer developed a chemical process by which alumina can be extracted from bauxite, a widespread and naturally occurring aluminum ore. Both the Bayer and Hall-Heroult processes are still used today to produce nearly all the world’s aluminum.
In the early 1900s, U.S. business leaders and industrialists quickly recognized aluminum’s superior properties. Power transmission lines and elevated train electrical wiring were among the first to benefit from the electrical advantages of aluminum. Aluminum found early industrial uses in engines, such as the one built in 1903 by the Wright brothers to power their first biplane.
Aluminum foil entered the market in 1910 and quickly became popular in providing air tight packaging for food and tobacco products.
Alloy development, begun in 1911, improved physical properties and opened new industrial fields. The Great Depression resulted in Works Progress Administration (WPA) projects that expanded hydroelectric generation capacity, which in turn increased production capacity of primary aluminum. During this time, the Aluminum Association was formed. The Association’s first meeting was held in New York City in 1935.
With the onset of World War II, aluminum became a key strategic metal. Primary uses of aluminum included the construction of aircraft frames, ship infrastructure, radar chaff and millions of mess kits. America’s supply of bauxite and readily available electricity for primary metal production resulted in soaring output that eventually topped the production levels of all of the Axis countries combined. On the homefront, aluminum recycling got an early start. “Tin foil drives” included an offer of free movie tickets in exchange for aluminum foil balls.
Following WWII, American industry shifted gears toward consumer products manufacturing.
The early 1950s saw the development of the iconic white-enamel/aluminum-frame washers and dryers. In 1959, Coors Brewing popularized the two-piece aluminum can with a pop-top lid. Equally innovative, a cash payment recycling offer was established for cans returned to the brewery.
In the 1980s, space shuttles were launched with an aluminum external tank and rocket boosters fueled with aluminum powder. Today, aluminum wiring is the top choice for utility and power transmission networks.
Steve Jobs recognized both the beauty and strength of aluminum, creating a thin, light product line of laptops, iPads and iPhones. What once was one of the most precious metals on earth, this “King of Metals,” is still growing in a number of applications. Aluminum-ion batteries, nanotechnology, advanced alloys for space vehicles—the aluminum industry now ushers the world into the second century of "The Age of Aluminum."
U.S. Aluminum's Economic Impact
The U.S. aluminum industry is a key element of the nation's manufacturing base. Strong, lightweight and recyclable, aluminum is a material uniquely suited to meet the needs and challenges of the 21st century. From increasing vehicle fuel efficiency to green building products to sustainable packaging, aluminum is well positioned in the U.S. and global markets.
For nearly a decade, the Aluminum Association has worked with research firm John Dunham & Associates to produce economic impact impact studies that capture U.S. aluminum jobs, wages, output and other information on an ongoing basis.