Wagstaff, Inc.
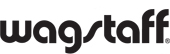
Wagstaff, Inc. is a 70-year-old manufacturing company that provides customized, advanced aluminium direct-chill solidification technology to rolling ingot and extrusion billet producers worldwide.
Wagstaff offers:
- Casting machines
- Mold tables
- Process automation
- Rolling ingot tooling
- Extrusion billet tooling
- Strong alloy capabilities
- Molten metal level control
- Worldwide service and support
Wagstaff has delivered more than 1,100 billet systems, 400 ingot casting systems, 225 ShurCast™ Casting Machines and 300 AutoCast™ Automated Casting Control Systems in 58 countries.
Facilities utilizing Wagstaff equipment are able to produce the highest quality billet and ingot with premium surface quality and metallurgical properties. Customers frequently ask for “Wagstaff billets” by name.
Beyond the hardware delivery, first-class customer service is included with every purchase of genuine Wagstaff casting equipment. From on-site start up and refresher training, to workshops held in convenient locations around the world, we are committed to delivering to the right tools at the right time.
Our Story
Founded in 1946, Wagstaff, Inc., a Spokane, Washington based manufacturer, provides machinery, technology, and service to enable aluminum producers to transform molten aluminum into solid shapes – “billets” (rounds) and “ingots” (slabs) using “direct chill” casting. The direct chill casting process uses water to chill molten aluminum in order to solidify it into desired shapes for further processing by sheet, plate, extrusion, rod, and forged part manufacturing. Around the world, aluminum producers look to Wagstaff for the know-how and equipment to safely cast aluminum.
Wagstaff develops, engineers, designs, and manufactures sophisticated molds, casting machines, automated systems, and ancillary equipment at our Spokane and Kentucky facilities and has commissioned systems in 58 countries thus far. With its expansive engineering department and state-of-the-art manufacturing capabilities, Wagstaff provides innovative, comprehensive solutions to aluminum producers for maximum quality and productivity in the casthouse.
With regional offices spanning the globe and a dedicated customer service team, Wagstaff is available and responsive to customer needs. Equipment installations around the world require a robust technical service team for after-sale commissioning and service. In addition to a core technical service team in Spokane, Wagstaff has representatives in Brazil, China, UK, The Netherlands, Australia, Croatia, Russia and Kentucky. These dedicated professionals regularly travel to customer locations to provide on-site installation assistance, service, and training.
In addition to its core aluminum business, Wagstaff has expanded its efforts to the custom machining industry with the Wagstaff Applied Technologies group. They utilize Wagstaff innovation and craftsmanship to provide performance-driven solutions in machining, process automation, and project management. Wagstaff Applied Technologies has experience serving nuclear, defense, semi-conductor, and OEM sectors.
Locally, Wagstaff is a contributor to many social programs and community action efforts. As one of the largest manufacturing facilities and prominent employers in the area, Wagstaff has committed to keeping its headquarters and core manufacturing operations in the Pacific Northwest. This strategic contribution earned Wagstaff the International Trade Alliance Exporter of the Year Award in 2005 and recognition as a key export business in the region.
Sustainable Practices:
Wagstaff, Inc. strives to be the worldwide leader in providing quality direct chill casting equipment to the aluminum industry. Our goal is to provide equipment that produces quality billet and ingot safely and efficiently. Sustainability can be seen in molds that use less water and oil for casting, resulting in lower water usage and less oil in the discharge waters. Metal used to fabricate casting tables can be recycled when the equipment has fulfilled its useful life. Refractory material may be reused in cement making and has been known to be reused in road building materials.
Safety is always a priority when casting. Wagstaff, Inc. supports a research and development team that is constantly working on new products, processes, and safer casting techniques that reduce the risk of severe injury or death. Also provided with our equipment is supervision of the installation, training for customers on the proper operation, maintenance, support for the equipment commissioning process, as well as providing ongoing technical support for our customers. Additionally, manuals with an emphasis on safety are provided for site preparation, installation, and operation and maintenance to insure the customer has readily available reference materials.
Wagstaff, Inc. has adopted a philosophy of reduce, reuse, and recycle. We have reduced the number of hazardous materials used in the manufacturing of our products. Examples include using steam and soap to clean parts instead of mineral spirits, and waste coolant is processed through an ultra-filtration unit to remove as much water as possible providing a more concentrated oil water mixture for recycling.
Recycling has always been a priority at Wagstaff. We recycle aluminum, steel, and other metals as well as cardboard, wood, oil, and office paper. These efforts have reduced the amount of materials going into a landfill.
Our efforts to reduce our carbon footprint include using energy efficient burners on our furnaces. Our research and development department, the primary user of water in our manufacturing facility, reuses water to the point where Wagstaff is classified as a non-significant user by the POTW. Electrical energy reduction is an ongoing effort. Wagstaff has reduced energy cost 5% per year over the last five years. Currently we are replacing our outside halide lights with LED lighting. This project will reduce our energy consumption by another 3% per year. Once completed, we will focus on replacing inside lighting with the LED lights. Additionally, all outside dumpsters have been covered to eliminate rain water from carrying contaminants to the storm drains.
Wagstaff, Inc. is dedicated to assist our customers in maintaining an efficient and profitable process for producing billet and ingot. Only through their efforts and ours can we be successful and sustainable in the future. We look forward to working with the Aluminum Association and its member producers to reach success in this endeavor.