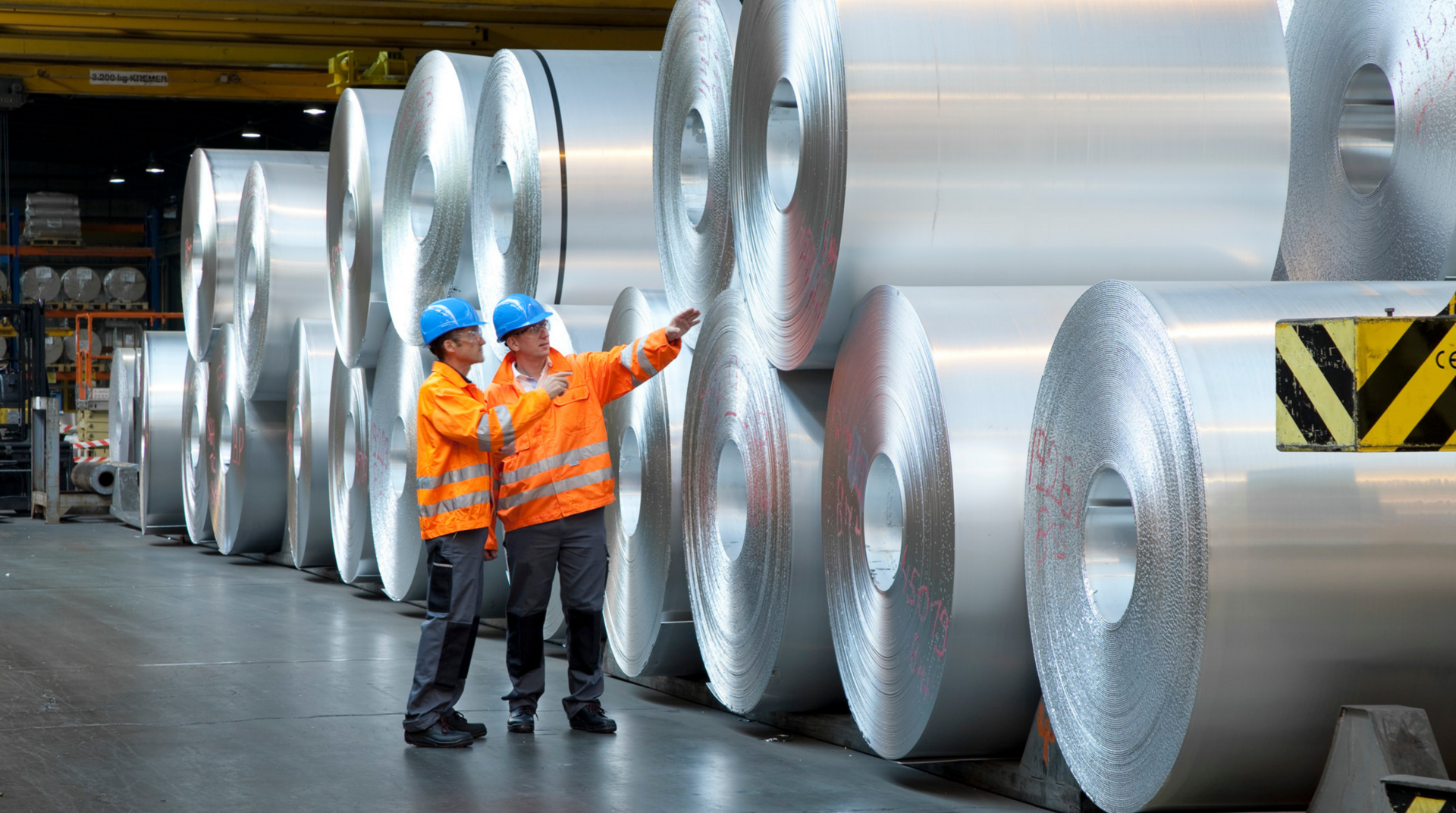
Processing 101
Between the production of aluminum from bauxite to well-known end products like buildings and beverage containers lies processing.
Between Production & End Product
Between the production of aluminum from bauxite to well-known end products like buildings and beverage containers lies processing. The processing of aluminum—using castings, extrusions and mill products—allows the industry to support end users to become more innovative with their designs and utilize greater technologies. Major types of aluminum processing include:
The process of casting aluminum
Casting is the original and most widely used method of forming aluminum into products. Technical advances have been made, but the principle remains the same: Molten aluminum is poured into a mold to duplicate a desired pattern. The three most important methods are die casting, permanent mold casting and sand casting.
Die casting
The die casting process forces molten aluminum into a steel die (mold) under pressure. This manufacturing technique is normally used for high-volume production. Precisely formed aluminum parts requiring a minimum of machining and finishing can be produced through this casting method.
Permanent mold casting
Permanent mold casting involves molds and cores of steel or other metal. Molten aluminum is usually poured into the mold, although a vacuum is sometimes applied. Permanent mold castings can be made stronger than either die or sand castings. Semi-permanent mold casting techniques are used when permanent cores would be impossible to remove from the finished part.
Sand casting
The most versatile method for producing aluminum products is sand casting. The process starts with a pattern that is a replica of the finished casting. Virtually any pattern can be pressed into a fine sand mixture to form the mold into which the aluminum is poured. The pattern is slightly larger than the part to be made, to allow for aluminum shrinkage during solidification and cooling. As compared to die and permanent mold casting, sand casting is slow process but usually more economical for small quantities, intricate designs or when a very large casting is required.
The extrusion process
Extrusion is a plastic deformation process in which a solid cylinder of aluminum (billet) is forced by compression through a smaller die opening. The billet is typically preheated to facilitate the deformation process.
Near infinite design possibilities
There are many factors in an extrusion process that influence the properties of the final product, including:
- Type, layout and design of the die
- Length of billet and type of alloy
- Temperature of billet and container
- Die and tooling temperature
- Speed of extrusion
These adjustable factors, coupled with inexpensive tooling, create near limitless possibilities for design. The strength, weight and sustainability of aluminum add to its appeal for manufacturing and construction applications.
Forming the end product
The aluminum extrusions formed right from the press are rarely seen in commercial applications. Extrusions typically undergo a number of fabrication and/or finishing processes to transform them into usable components, such as an auto part or construction material. The fabrication process generally starts with cutting the extruded length, followed by punching, machining, bending or welding.
Open-die forging
Ideal for processing large pieces of aluminum, open die presses do not constrain the aluminum billet during the forging process and utilize flat dies free of precut profiles and designs. Aluminum blocks weighing up to 200,000 pounds and 80 feet in length can be open-die forged to create large aluminum components with optimal structural integrity. While welding and joining techniques are useful in creating large components, they cannot match the strength or durability of a forged part. Open-die forgings are limited only by the size of the starting stock.
Closed-die forging
Closed-die forging, also known as impression-die forging, can produce an almost limitless variety of shapes that range in weight from mere ounces to more than 25 tons. As the name implies, two or more dies containing impressions are brought together as forging stock undergoes plastic deformation. Because the dies restrict metal flow, this process can yield more complex shapes and closer tolerances than open-die forging. Impression-die forging accounts for the majority of aluminum forging production.
Rolled-ring forging
When industrial applications call for a high strength, circular cross section component, there is no match for rolled-ring forging. The process typically begins with an open-die forging to create a ring preform, shaped like a doughnut. Next, several rollers apply pressure on the preform until the desired wall thickness and height are achieved. Configurations can be flat, like a washer or feature heights of more than 80 inches. Rings can be rolled into numerous sizes, ranging from roller-bearing sleeves to large pressure vessels.
Aluminum Powder 101
Production of aluminum powder
Aluminum powder was originally produced by using a stamp mill to create flakes. In the 1920s, E. J. Hall pioneered the process of spraying molten aluminum to make powder droplets. Today, molten aluminum is sprayed under high pressure to produce a fine granular powder. Two types of powder (nodular and spherical) can be produced, depending on the type of atomizing gas that is used to "blow" the molten aluminum from a nozzle tip.
Lighter building products
Aluminum powder is also a key ingredient in the production of "fly ash bricks" (bricks made from fly ash, water, quicklime, cement and gypsum). Builders save about 30 to 35 percent of the weight of structural steel and concrete, as these blocks significantly reduce the load placed on the building’s frame.
A key component of solar cells
Aluminum powder plays a vital role in the fabrication and performance of solar cells. A film paste made from aluminum is applied to the back side of silicon to be used in solar cells. The paste is metallized and screen-printed to create the electrical conduction properties necessary for the solar cell to function properly. Continuing improvements to reduce the granular size of powder (referred to as "superfine") will increase solar cell efficiency and reduce manufacturing costs.
Aluminum Pigment 101
Production of aluminum pigments
Aluminum pigments are produced almost exclusively using a wet-milling process that involves mineral spirits or other solvents. When aluminum powder is milled into a pigment, the geometry of the particles forms different shapes. For example, pigments used in plastics come in three different shapes. They resemble a flat cornflake, a flat ellipse and a sphere. Mirror-like pigments are produced through a vapor deposition process when a thin aluminum layer is deposited on a carrier film. The metallized film is run through a solvent tank where the release coating is dissolved. The remaining aluminum layer is removed to form coarse reflective aluminum pigment flakes.
Aluminum pigments bring color and sparkle
Aluminum pigments appear to have color because they absorb some wavelengths of light more readily than other wavelengths (selective absorption). In contrast to a dye, a pigment generally is insoluble and will not combine with the substrate. This is a vital advantage when absorption-prone materials are used. The appearances created by aluminum pigment range from metallescence (a colored pearlescent effect), a "liquid metal" appearance, a high or pinpoint sparkle and the glitter effect. Pigments can appear low-sheen or exceptionally bright, depending on the surface polish. These light-absorption and reflective factors contribute to the different appearances of paints and coatings used in the automotive industry.
Holidays sparkle with aluminum pigment & powder
Aluminum powder was used in early photography to create the bright flashes necessary to take pictures. Today, it is one of the key materials used in the manufacturing of fireworks.
Christmas tree ornaments are commonly accented with aluminum pigments. Their metallescent, liquid metal, pinpoint sparkle and glitter effects are created by aluminum pigments (with some help from Santa, of course).
Producing rod and bar
Aluminum rod, bar and wire products can be produced in several ways. One method is similar to rolling sheet. A long, square ingot is heated, progressively reduced in cross-section by passing it through a series of rolls, and then coiled. The coils are heated and, if slated to become wire, pulled through smaller and smaller dies. Extruded aluminum can also be drawn directly into bar, rod and tube formations and then progressively thinned through dies.
Producing wire
Made from aluminum rod, wire is, by definition, less than 3/8 inch in diameter. Electrical conductor is made by stranding several wires into a single piece. Electrical conductor rod can also be drawn and stranded directly from molten aluminum.
Applications
Electrical transmission lines are by far the largest application for aluminum rod and bar products. This is a market in which aluminum has virtually no competition from other metals. Aluminum is simply the most economical way to deliver electrical power. Aluminum wire and cable are also used almost anywhere there is an electrical impulse to conduct—in commercial buildings, machinery and equipment, transportation and consumer durables. Wire and cable are used for little jobs we seldom think about, such as the non-rusting staples in tea bags and re-twisting twist-ties.
Producing aluminum plate
Rolling begins with preheated sheet ingots that can weigh more than 20 tons. As the size of rolling mills has increased, so has the size of these ingots, but a typical ingot is approximately 6 feet wide, 20 feet long and more than 2 feet thick. The ingot is first heated to rolling temperature and fed into a breakdown mill, where it is rolled back and forth until the thickness has been reduced to just a few inches. The slab can be subsequently cold rolled or may be heat-treated to increase its strength. The highest strength alloys are heat treated and rapidly cooled to room temperature, after which they are stretched to straighten and relieve internal stress built up during rolling and heat-treating. They are aged naturally at room temperature or artificially aged in a furnace to develop the desired combination of strength and corrosion resistance. Finally, the plate is trimmed to final size. Plates produced in this manner may be used at full thickness, but are often machined into a variety of simple to complex shapes.
From plate to sheet and aluminum foil
The production of sheet or foil usually starts out the same way as plate but the slab is further rolled through a continuous mill to reduce thickness and wound into a coil at the end of the line. These coils are subsequently cold rolled, from one to several passes at cold rolling mills. Coils may be heated in a furnace to soften it for further cold rolling or produce the desired mechanical properties. Cold rolling is the last step for some sheet, but other types (referred to as heat-treatable) are subjected to further elevated-temperature processing to increase their strength.
Some sheet and foil products may also be produced using the continuous casting process in which molten metal enters the caster, which produces a hot rolled coil, thus bypassing the ingot casting and hot rolling steps.
Aluminum plate applications
Plate is used in heavy-duty applications such as those found in the aerospace, military and transportation product manufacturing. Aluminum plate, machined to shape, forms the skins of jets and spacecraft fuel tanks. It is used for storage tanks in many industries, in part because some aluminum alloys become tougher at supercold temperatures. This property is especially useful in holding cryogenic (very-low-temperature) materials. Plate is also used to manufacture structural sections for railcars and ships, as well as armor for military vehicles.
Aluminum sheet applications
Sheet, the most widely used form of aluminum, is found in all of the aluminum industry’s major markets. In packaging, sheet is used to manufacture cans and packages. In transportation, aluminum sheet is used to manufacture panels for automobile bodies and tractor trailers. Sheet is used in home appliances and cookware. In building and construction, it is formed into products including siding, gutters, roofing, awnings and carports. Sheet aluminum can be color-anodized to black, gold, red, blue and hundreds of other colors. It can be etched to a matte finish, polished to a sparkling brightness or textured to resemble wood and painted.
Aluminum makes the recipe
Recipe success may depend on the use of sheet aluminum. Because some bakeware conducts heat poorly, while others discolor certain food, many recipes specifically recommend the use of aluminum sheets and foil. They are renowned for even heat distribution and durability.