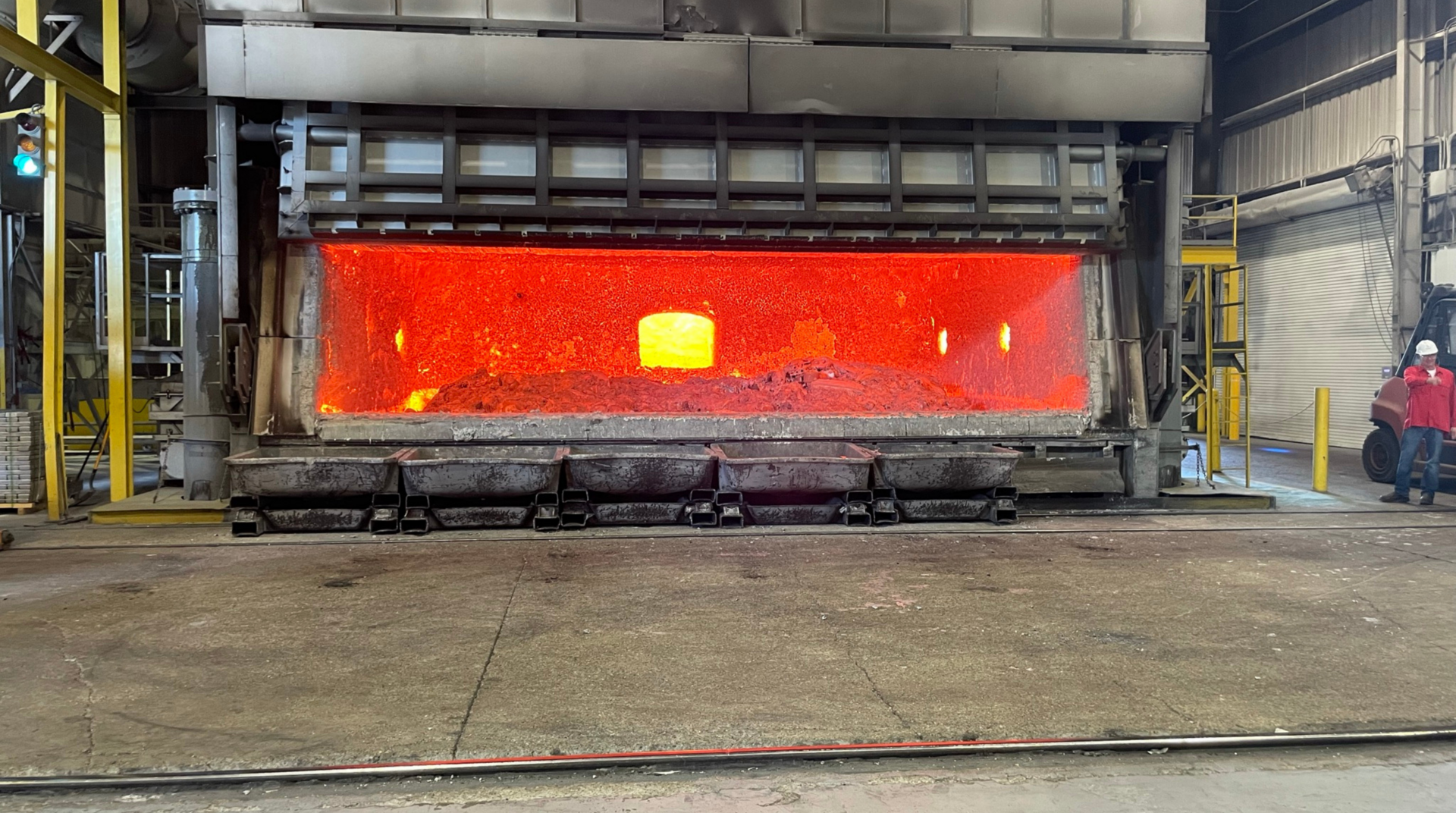
Secondary Production 101
Secondary Production is the process of recycling aluminum scrap into aluminum that can be used again—an environmentally sound process that is around 95% more energy efficient than primary production.
Making Old New Again
Segregation & Alloying
The secondary production process begins with extracting used aluminum from waste streams and getting it ready for recycling. Because of the energy savings benefits it provides, aluminum scrap is a most valuable commodity. Scrap segregated by chemical composition, or alloy, maintains the highest value while scrap containing a mix of alloys and other materials has the lowest. New technologies, such as Laser Induce Breakdown Spectroscopy and Color Sorting, can separate aluminum and remove contaminants to improve the quality and value of the scrap. This fine-tuned recycling process allows aluminum cans to be recycled over and over again in a true closed loop process.
Into the furnace
Once the scrap is collected and sorted, it is placed into a melting furnace and turned into molten aluminum at temperatures ranging from 1300 to 1400 degrees Fahrenheit. This molten aluminum may be kept in its liquid state or cast into large slabs called ingots or billets. In some cases, alloying elements are added to the liquid aluminum in order to produce the desired metal for a specific product type. Aluminum ingots may be rolled back into a sheet product (like can or auto body sheet) while billets can be extruded into a shaped product, such as window frames or an Apple computer case.
Infinite possibilities
Additional metals and compounds are often added during the secondary production process to achieve the right alloy “recipe” for the finished product. High performing products such as building materials or automotive parts can be recycled from other high quality aluminum products, such as aircraft components. And since aluminum never loses its performance or strength during the recycling process, the same piece of aluminum can enter the secondary production process time and time again, multiplying the cost savings and environmental benefits.