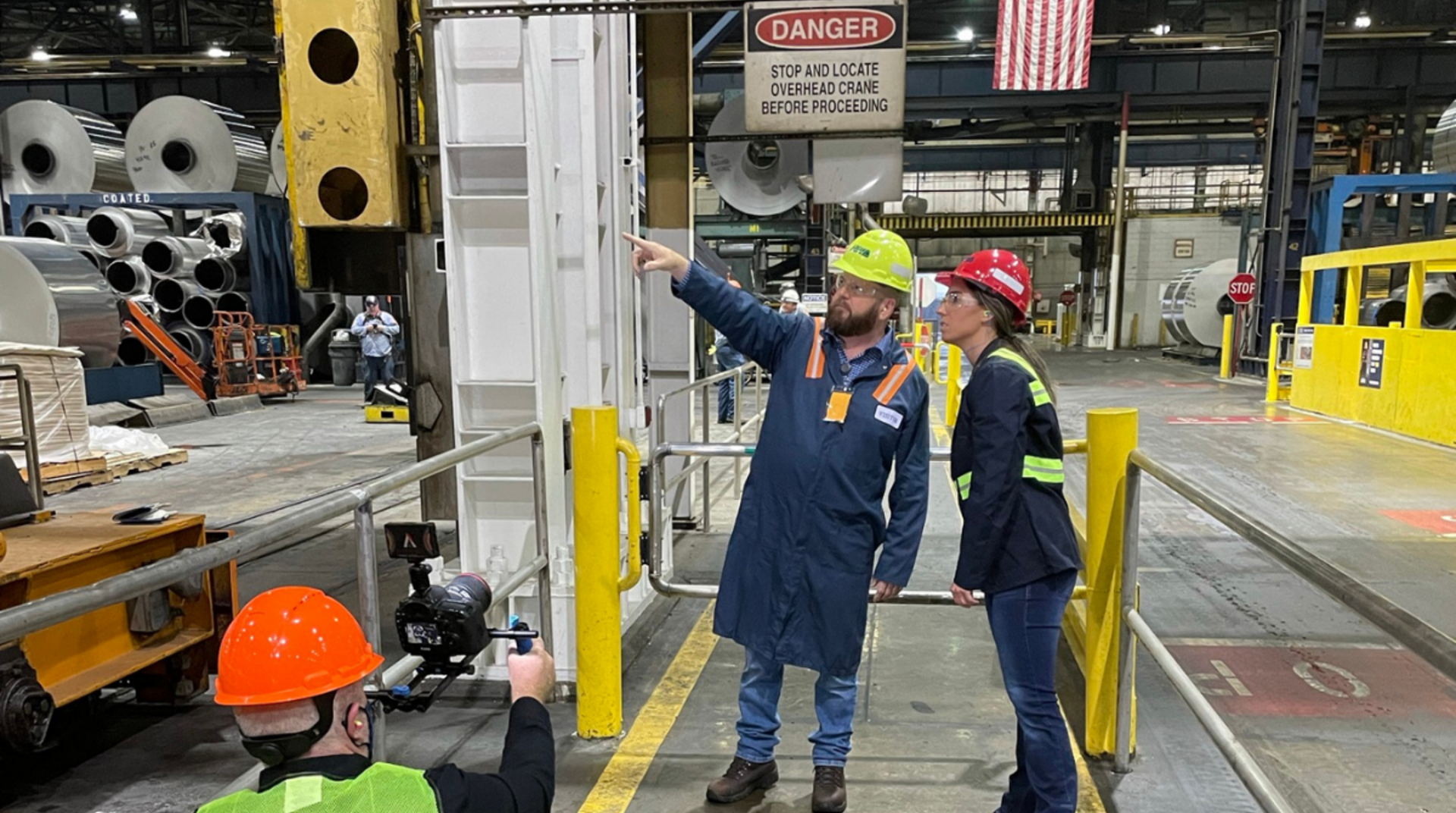
How America Works with Aluminum
Mike Rowe of Dirty Jobs fame hosted a deep dive look at aluminum production and recycling for an episode of his series How America Works. He found that U.S. aluminum is in a class of its own.
“The Most Important Metal in the World”
Mike Rowe’s How America Works crew visited Logan Aluminum – one of America’s largest aluminum production facilities based in Russellville, KY. Logan ships 6 million pounds of aluminum product everyday (up from 5 million pounds/day just a few years ago) to serve markets including aluminum beverage cans. (Americans go through 200 million of those everyday!)
Which explains why the metal is in such high demand. In fact, the United States uses more than 10,000 metric tons of it every day – more than enough to make four Boeing 747s every hour of the day.
Aluminum, Rowe concludes, just might be the "most important metal in the world."
“Of all the metals that reinforce our nation, aluminum comes in a class all its own. It doesn’t rust. It’s lightweight. And in spite of that, it’s incredibly strong.”
- Mike Rowe
Behind the Production
Across the United States, dozens of recycling plants like Logan transform scrap aluminum (from old buildings, cars, trucks, used beverage cans and more) into brand-new metal. Reusing scrap aluminum is cost-effective and better for the environment. Aluminum is infinitely recyclable, with nearly 75% of all aluminum ever produced is still in use today.
An integrated facility, Logan receives baled aluminum scrap to shred and process for melting on site. The procedure includes removing dross (the impurities in newly molten metal) and adding new (or primary) aluminum and other chemicals to meet end user specifications. The scrap "must be melted down, cast, and rolled out by quitting time."
To do that, the melted aluminum is distributed into 25 feet vertical shafts beneath the floor to create massive 30-ton ingots – each representing about $75,000 worth of aluminum. After the metal has cooled sufficiently, a reversing mill compresses the three-foot-thick ingots into the width of a sheet of paper to enter yet another mill for final processing.
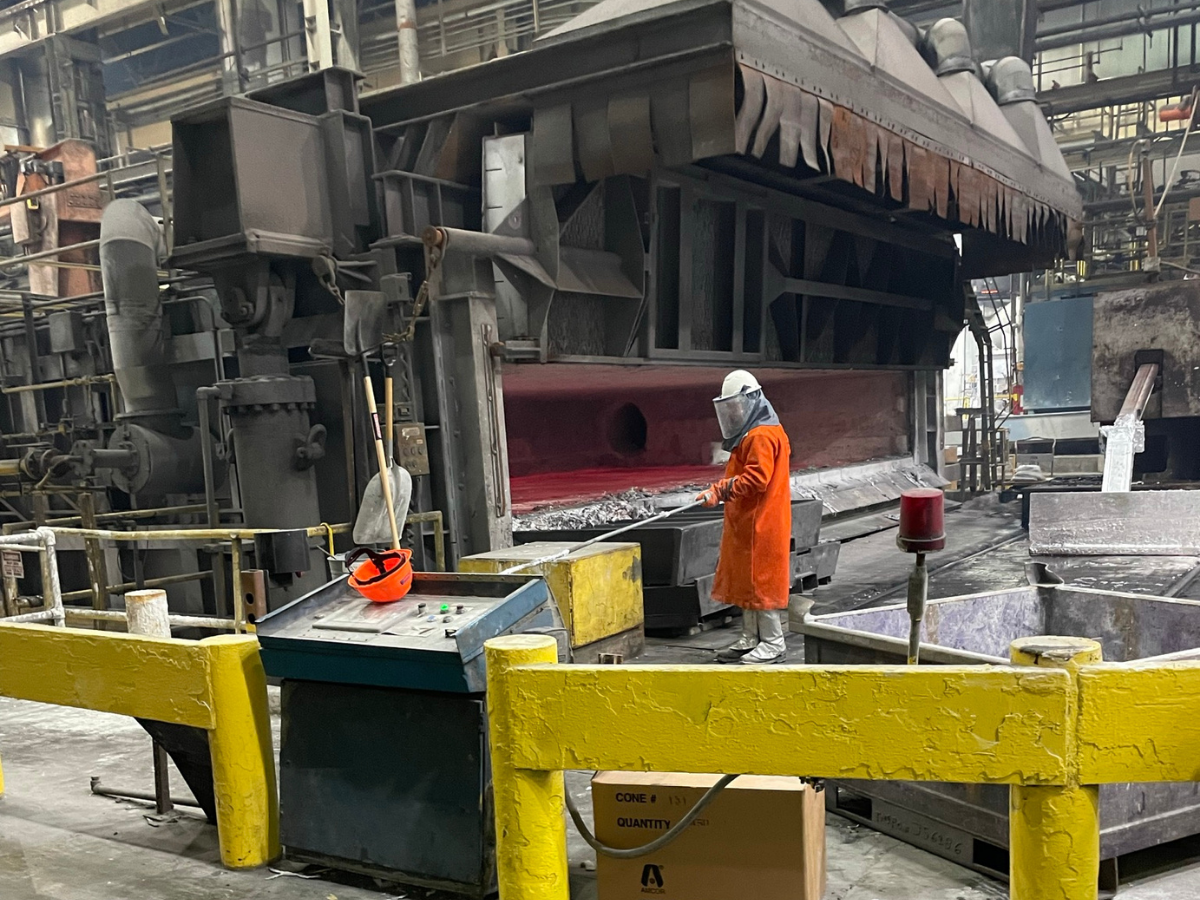
Keep Rolling
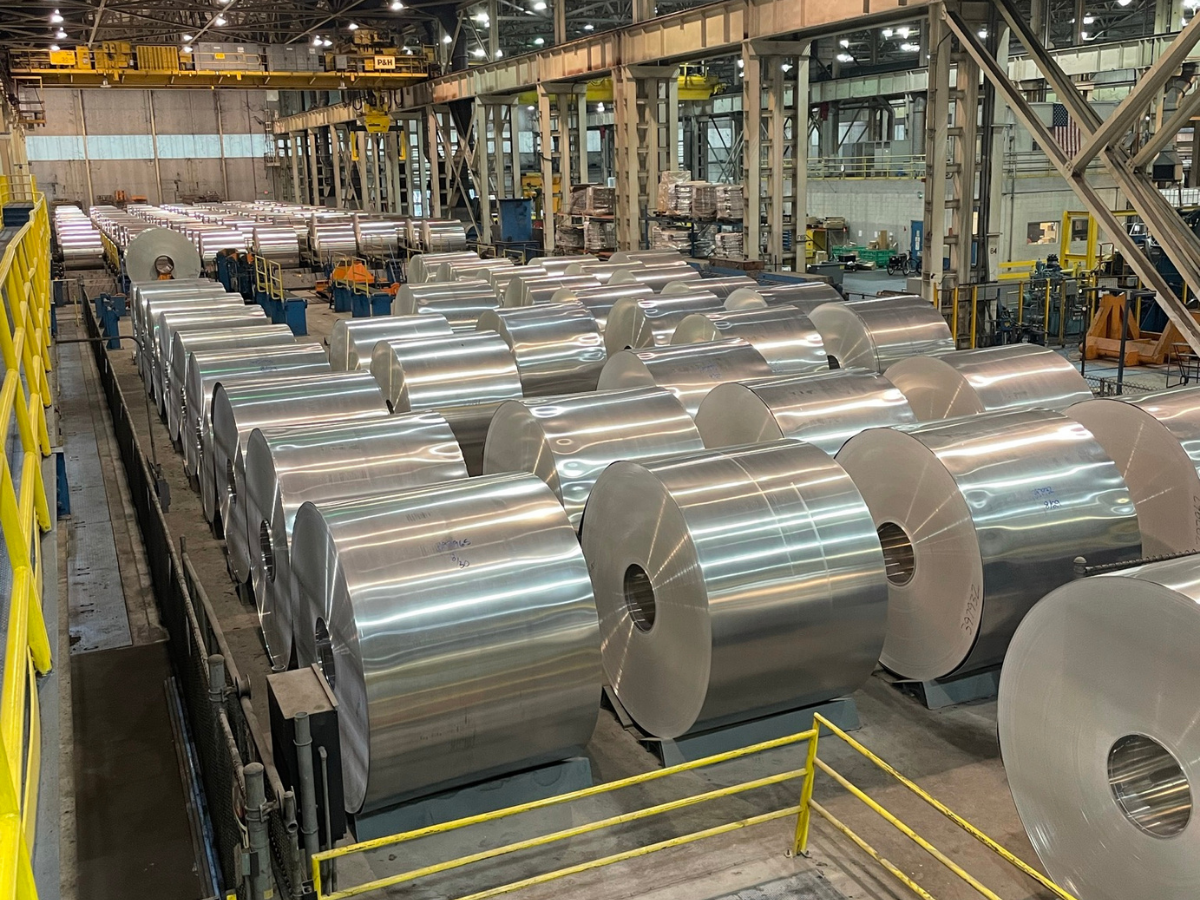
The next step of the process brings the rolled aluminum sheet to a finishing mill. There, the metal is rolled once more into the precise gauge needed for whatever its intended end use.
In addition to aluminum cans, Rowe notes, "There's also the automotive industry, powerlines, skylines, appliances, ships, trains, foils and countless other applications that would be crippled without this almighty metal."
Want to learn more?